Tanker Boiler Economizer
Tanker Ship Economizer Boiler
A ship's boiler, also known as a steam boiler, is a machine designed to generate steam, which is used for heating systems or propulsion. The economizer boiler, which operates by utilizing waste exhaust gas heat from the chimney, is a cost-effective technology that turns wasted heat into an energy source. This technology is a choice for the present and the future, offering low operational costs that can cut operating costs by 30 to 40% before using our proposed system.
Uses of a Boiler on a Ship The main function of a ship's boiler is to produce steam. The steam produced by the boiler serves as a source of heating for the hot water room, fuel heating, and for ships (Residue, MFO, CPO Barge, Crude Oil Tanker). It can also be used to drive a steam turbine, which is the main propulsion engine of the ship. The ship's boiler heats the fluid in the tank, converting it into steam or a Heat Transfer Oil Heater system. Once the steam is generated or the oil is heated, it is directed to the components that require it, either to drive a turbine or to provide heat (heat transfer steam/heat transfer oil tanker).
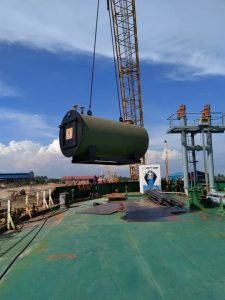
The function of a ship's boiler is to generate power for the main and auxiliary engines, for heating equipment (room heating, fuel, oil cargo, etc.). On tanker ships, it is used to heat Crude Oil and Crude Palm Oil (CPO) to maintain the temperature and ensure that the CPO yield doesn't decrease in volume. It's also used for cleaning the oil tank (Tank Cleaning).
Additional equipment for ship boilers includes
- Feed Water Tank (Deaerator tank)
- Feed Water Pump (Boiler feedwater pump)
- Water Softener
- Dosing Pump
- Water Regeneration Resin
- Fuel Tank
- Steam Header (Steam/oil heater distributor)
- Economizer (utilizes chimney exhaust gas to heat boiler feedwater as an energy source)
- Steam Flow Meter
- Fuel Metering
- Boiler Feedwater Metering
By 1835, there were about 700 steam-powered ships in use in the United States. Steam pressure in low-pressure steam boilers, just a few kilograms above atmospheric pressure (saturated steam boilers), took the form of a rectangular box with only a square furnace and winding smoke pipes, which were large enough for a person to pass through for pipe cleaning. The smoke pipes were made of copper or iron plates, and coal and wood were common fuels. The famous Monitor ship of 1861 was equipped with two
fire tube steam boilers,typical steam boilers of the time. As a result, the world was captivated by the value of steam-powered ships for naval service after the encounter with the CSVirginic (ex-Merrimac).
The demand for more power and speed led to the development of better steam boilers. In 1861, the U.S. Navy cruiserNavi,Wampanoag,represented the pinnacle of marine engineering achievement during the Civil War era. A good ship was a fast steamship, and during trials, it reached a maximum speed of 19.5 knots. The engine's circulation was obtained by heating four steam boilers and eight vertical water tube boilers. In reality, the combination of water tubes with a cylindrical furnace similar to fire tube steam boilers and a return to fire tubes. The boiler pressure was maintained at around 90 psig.
After the Civil War, metallurgy and engineering continued to advance, resulting in the fire tube/pipe
steam boiler or "Scotch" boiler becoming the most popular. In the late 1800s and early 1900s, Scotch steam boilers were usedfor pressures up to 250 psig and steam temperatures up to 650 F. They were tolerant ofpoor water quality, lubricating oil, and common mistakes, making them ideal for use withsteam engines popular at the same time. When equipped with superheaters and air heaters,Scotch steam boilers achieved efficiency of around 75 to 80%.
The development of steam turbines led to high-pressure steam temperatures, andScotch-type steam boilers were replaced by water tube steam boilers. Initially, water tubesteam boilers were prone to failure due to inadequate circulation, poor water treatment,and inadequate tube arrangements, making them challenging to repair.The first water tube steam boilers were of the coil type, laterdeveloped into straight drums to avoid maintenance or cleaning difficulties.First tried on the steamship Reverie in 1889, this concept rapidly developed for naval service in the United States and Great Britain, as well asfor merchant ships. The basic requirements of RADM George W. Melville, Arctic explorer,for this type of marine steam boiler are as follows:From the study, I conclude that water tube steam boilers must have, among othercharacteristics, the following:
-Adequate storage space.
-An adequate water supply, ensuring a continuous water supply;
-Accessibility for cleaning and firing.
-Straight tubes, free from joints, thus resistant to testing.
-No cast metal, either iron or steel, so it can withstand pressure.
-Ability to generate steam rapidly.
-Competitive high efficiency.
Part interchangeability, so repair materials can be obtained anywhere,ability to withstand severe conditions without damage. It should have rough and not sosmooth construction to be operated by skilled mechanics.1, Safety against tube explosion, meaning that only parts of the steam boilerthat can be damaged. The design performance improved over the years by using 2-inchtubes passing three gases, while 1 1/4-inch or 1-inch tubes are passed by one gas.2, to improve efficiency and capacity.The basic design level is shown by the fact that many of these boilers are stillin service for propulsion purposes.
Water tube steam boilers, which had been experimented with since the early days, finallyemerged in a more practical condition in the 1890s. Leadership encouraged the developmentof high-speed torpedo boats. High pressure, about 250 psig, could make natural circulationin both types of water tube steam boilers unnatural.Forced circulation of the steam boiler can lead to issues such asfeedwater control, start-up, maneuvering, and lack of pump performance."Therefore, the main effort of steam boiler designerswas recommended for the development of natural and simple water tube steam boiler circulationin terms of operation and maintenance.
Natural circulation of water tube steam boilers hasmany forms. Early designs were generally of single-furnace with three double-absorptiondrum types with superheaters on one side. As steam temperature increased, it was necessaryto use an economical method to control steam temperature. This was initially doneby using a separate superheater where the combustion rate decreased as it moved towardsthe rear of the steam boiler.Subsequently, dual-furnace steam boilers were developedwhere steam temperature was controlled by varying the combustion rate in two furnaces.This early configuration used double-speed with a very hot heating section located in one gaspath. Furthermore, single-absorption dual-furnace steam boilers are shown to have beendeveloped. The design of this type of steam boiler is installed in almost all combat shipsbuilt for the U.S. Navy in World War II [2].
With the development of steam turbines capable of using full steam temperatureduring operation in the aft, it became possible to reduce the weight and size of steam drumtype boilers. The result is a two-drum single-furnace steam boiler with a separate superheater,located near the combustion furnace, providing relatively constant steam temperature duringvarious operations due to a combination of convection and radiative heat transfer characteristics.The latest shipping and naval steam boilers are a solid link in the evolutionary chainof boiler types.While many variations of these boiler types have been used worldwide, the typesdiscussed are representative enough and provide adequate backgroundfor understanding the types of steam generators and their characteristics.
In the last 100 years, steam pressure and temperature have increased from 30 psig saturatedto 870 psig - 950 F in most merchant ships, and up to 1200 psig - 1000 F maximum (950 F nominal)in most post-World War II naval combat ships. Most high-power steam installationsoperate at 1500 psig - 950 F, and in some cases heat up to 950 F, appear feasible.In most cases, the use of water cooling in the furnace is used toreduce refractory maintenance. Economizers and single air heaters, or combinations, are usedto achieve the desired overall boiler efficiency. Attemperators are used to control steam temperatureover a wide operating range, thus improving turbine performance. Desuperheatersare installed to help produce low-temperature steam for ship-wideuse. Bunker C residual oil is the most commonly used fuel incommercial applications, while marine diesel and other light fuel oils aremost commonly used in naval applications. Steam-atomizing oil burners, firstused on ships in the late 1800s, have returned to supportwith the emergence of cheap, high-capacity evaporators to supply required water.The type of nozzle for providing a very wide operational range, results in a loss of distilled water, istoo great a penalty to pay for profit.However, improvements to reduce heating consumption,along with abundant distilled water, have led to extensive use, especially in automatic boilers.
Two-drum separated-furnace boilers, or D-type boilers, are often referred to asSteam Drums, typically consist of a steam drum and water drum connected bywaterwall and boiler storage tubes. Superheaters are placed between the waterwall and theboiler body and may have tubes arranged both vertically and horizontally,depending partly on the most suitable engine configuration. Ifneeded, steam temperature can be controlled by desuperheater control orattenuator located on the steam or water tank. The location of oil burnerministers is often dependent on the engine configuration and may be on the front wall(most conventional), roof, or side wall. Figures 4 and 5 show some of these variations.Most installations use some form of air heaterswith economizers. The type and proportion of additional heat exchangers depend onthe cycle arrangement. When two-stage heating is selected, steam air heating andeconomizers are often used. In steam air heating, low-pressure steam (40-65 psi)condenses to heat the incoming air.
Where three or four-stage heatingis used, it is generally advantageous to use regenerative-type or regenerative-typeair heaters. A small economizer can be used in these cases to hold theair heater to a practical size. Air heaters exchange heat from gas to gas andtend to be quite large due to the relatively low heat transfer rates.Natural circulation is used exclusively in two-drum boilers and dependson downcomers, which may be internal (heated) variations in low-rated unitsor external (heating) in various high-rated merchant and naval units.
Economizers adalah kekuatan disuplai oleh pompa umpan boiler dalam semua kasus.Membersihkan permukaan eksternal yang terkena bahan bakar minyak abu jelagasemut dapat dilakukan dengan cara sootblower uap. Letaknya berada di zona superheater yang ditarik untuk memberikan daya pembersih yang cukup untuk menghilangkan terak.Perlindungan dari suhu gas yang tinggi di daerah ini disediakan dengan menariknyaketika keluar dari layanan.Sebuah desuperheater tambahan dipasang dalam uap atau air drum kebanyakankapal untuk memasok uap suhu rendah untuk tujuan selain propulsi utama.Rumah yang mengelilingi bagian tersebut bertujuan dan membentuk amplop kedapgas mengandung produk sampingan dari pembakaran. Konstruksinya bervariasi, namunrumah ganda umumnya digunakan untuk menghindari kemungkinan kebocoran gas buang ke ruang mesin. Dimana rumah tunggal digunakan, sendi ekspansi, pembukaanakses, dll, disediakan dengan segel bertekanan udara untuk mencegah kebocoran.
In the reheating cycle, steam is generated at high pressure, heated ina conventional boiler and superheater elements, and then expanded through high-pressureturbine elements to the inlet pressure of the reheater. It is then heated, reducingpressure, and expanded through low-pressure turbine elementsFor smooth and reliable operation, provisionmust be made to protect the reheater from overheating during maneuvers andrear part operation when the reheater flow is reduced or absent. The boiler design issuitable for reheating; therefore, it is somewhat more complicated than superheaterelements for a conventional non-reheat cycle.Steam reheating becomes more attractive with increasing installed horsepower. Fuel storage that can be obtained by reheating, which issufficient to justify a more complex engine. For the most part, steam generatorsfor supplying heating plants have been adapted from two-drum separated-furnace boilers. One or two furnaces can be used. The single-furnace conceptutilizes gas flow paths divided outside the furnace with superheaters and reheating deviceslocated in separate sections. The gas flow in this part is regulated by dampers, thuscontrolling superheater and steam temperature heating.
They then merge into anadditional heat exchanger. By burning all fuel in a single furnace,oil burner and forced-air supply system designs are simplified.Figure 6 illustrates this type of boiler. In divided-furnace boilers, twofurnaces are used, one furnace supplies heat to the superheater and the other furnacethe superheater hot part. Some designs combine parts of the superheater(called primary superheater) in the reheater zone to provide additional protectionfor the reheater and to obtain the desired steam temperature characteristics.The gas flowing from both the reheater and superheater elements convergesinto the main generator tube bank, and a single gas flow path is maintained throughauxiliary heat exchangers such as in a single-furnace design.
Since the first boilers were used on ships, marine boiler designers have investigatedand experimented with various ways to reduce the size and weight of the boiler.A boiler set up for the natural circulation of water and steam requires a pressure drop,which can only be obtained by installing sufficient downcomers and risers.This is detrimental because it affects the size and weight. By providing a pump for both addingor replacing natural circulation, small and light boilers can be designed to provide steam output.Circulation in boilers is said to be controlled or forced. The main advantage is that very small-diametertubes with high resistance to flow can be used in surface heating arrangements, and the location of the Steam Drumwhich is not suitable for natural circulation. The biggest weakness is the circulation pump itself, whichcan potentially become a source of trouble and maintenance.LaMont boilers, shown schematically, are an example of the typical type of forced circulation boiler.
While used outside, it has not been widely applied in marine applications in the U.S.LaMont boiler uses a single drum in which the heating surface mixture of steam and water is discharged.Circulation is supplied by gravity from this drum and the force of water through the tube surface continuouslygenerated, consisting of a number of tube circuits arranged between distributingheader and steam drum. Each tube inlet is equipped with a hole to balance the flow resistance in various circuits.This is necessary toobtain adequate water flow in each tube, depending on the expected heat input. The furnace, oil burners, superheater,economizer is similar to natural circulationand is available as a packaged unit. The size of this type of boiler does not suit it forlarger installations but has been used on ships of less than 10,000 SHP. Thecircuitry was located close to the wall were each one could beblown out with water to remove soot when soot blowers were out of service.
For certain auxiliary equipment, a steam source of moderate pressure and temperature is required.Although an auxiliary boiler is one source for steam, high-temperature water (HTW)systems are often preferred. The necessity for high-pressure steam arises from largeshafting and ship-propelling turbines. Fuel oil systems can be expensive. Boilersfired with gas, oil, or waste heat can also be used to produce HTW, which is then used toprovide some of the heating and cooling. As the ships' services have become more diversifiedmore of them are of a size and weight that can be accommodated. A high-temperature water boileris one that provides steam to the propulsion turbines. A typical high-temperature water boileris illustrated in figure 8, complete with the necessary valves, pumps, andexpansion tanks.
This type of boiler has the furnace below the horizontal tubes to give a compact assemblyof hot gas in the upper part of the furnace. The hot gas will then flowup through the tubes and out of the stack. With this flow pattern, this type of furnace is sometimescalled a bottom-fired boiler. The furnace will be fired with anoil or gas burner and use a superheater to produce the temperature of the steam that isrequired. For larger capacities, this boiler can be of water-tube design or fire-tube design.The water-tube design was used on smaller-capacityunits. Such boilers were often used in ships of more than 10,000 SHP. Theburners on the furnace's sidewall can be removed byhand without the removal of the steam drumsburner in such a way that each soot blowercould be removed without interfering with the operations of any other soot blower.The steam drum will be as located where each one could be blown out with water to remove sootwhen soot blowers were out of service.
There are those marine designers that attempt to eliminate the steam drum byusing a water tube boiler design. The basic idea is to isolate a single water-tube fromthe rest and then superheat the steam produced in the individual tube. The water flow ishigh and there is little opportunity to accumulate deposits. Figure 9 shows such aboiler.
The structure of the water tube of the boiler is arranged to ensure that the hottest gases flow close to the water surface in the hot water economizer, furnace, and superheater arrangements. The entire assembly overhangs the stack, with gas-flow areas for each arrangement. Each area will be accessible with soot blowers. This boiler type is referred to as a steam generator.As with the other circulating-water-tube boiler types, the bottom of the furnace will have water tubes that are constructed from the refractory wall. Figure 10 shows the arrangement of the steam drum in a large unit, where the circulation from the water drum is passed through the superheater, economizer, and then to the steam drum. The entire furnace, reheater, superheater, economizer, and soot blower will be shipped as an assembly.
Cooling exhaust gases with inlet combustion air is one of the oldest concepts for improving boiler efficiency. Furthermore, hot air provides an additional beneficial effect by ensuring rapid and complete combustion of the fuel. This can be crucial in the use of relatively small furnaces in marine boilers.Air heaters consist of two broad classifications: recuperative and regenerative. In recuperative types, heat from combustion products passes through a partition that separates the combustion products from the air. Tubular and plate-type air heaters are examples of recuperative air heaters. In tubular heaters, tube wall transfers heat from gas to air. In plate-type heaters, air and gas are separated by plate elements that convey heat. However, recuperative heaters have largely been replaced by regenerative types.In regenerative air heaters, the initial heat is stored within the heater structure as it passes through the hot gas flow. This heat is then transferred to the air as it flows through the structure, as shown in figure 14. This type consists of heating elements arranged closely packed in a rotating frame. The frame's speed remains constant and is controlled by a small electric motor. The frame speed is chosen so that the elements can absorb heat from the gas with a good temperature difference and, at the same time, heat the inlet combustion air as high as possible.
The selection of air heaters is in the cold air zone and also "sees" the coldest gas. They are usually arranged so that the heat transfer surfaces can be easily cleaned and easily handled by the so-called "basket" when corrosion and fouling may occur there. These baskets can be provided, in addition, with ceramic layers similar to porcelain enamel for protection against the corrosive effects of sulfuric acid, which can also be formed from combustion products. Air bypasses can be provided to avoid excessive cooling and condensation of exhaust gases during low-load and idle or cold weather conditions.Steam air heaters (fig15) are used where the pressure is sufficiently low, low-temperature steam is available, and it is desired to preheat the combustion air. If exhaust gases or steam turbines are used, there is little improvement in the overall cycle efficiency. The heater consists of coiled tubes equipped with extended surfaces, typically consisting of wound material strips, welded or brazed to copper-nickel tubes. The tubes are shaped and arranged between the inlet and outlet. Steam is supplied and condensed by incoming cold air, and the condensate is removed by steam traps. The latent heat of this flow, which would not be rejected in the condenser, is returned to the boiler through the hot air.
Must Read
1 |
Linear Burner For Scorching Machine |
2 |
Boiler Biomass Gasification |
3 |
Biomass Boiler Systems |
4 |
BOILER CLASSIFICATION |
5 |
Hospital Steam Sterilizers |
Info
Don't hesitate to contact our sales team to get more information about our products and services. Our sales team is ready to assist you in selecting the right boiler product for your industrial needs and providing competitive price quotes.